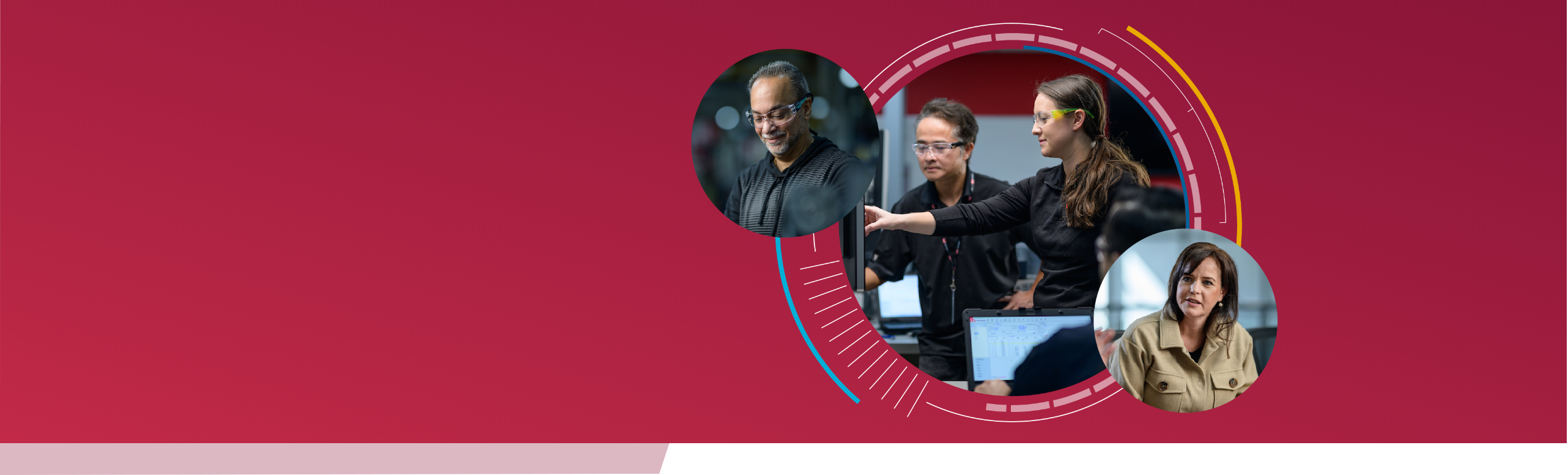
Ignite Your
Full Potential
Lorem Ipsum has been the industry's standard dummy text ever since the 1500s.

Lorem Ipsum has been the industry's standard dummy text ever since the 1500s.
OWN YOUR CAREER
At ITW, our people are empowered to think and act like entrepreneurs.
Starting on day one, you will be trusted and supported to embrace autonomy, make decisions, innovate valued solutions and drive results, providing you with exceptional personal and professional growth opportunities. No matter which of our seven segments or 80+ divisions you start in, you can grow your career at ITW.
Starting on day one, you will be trusted and supported to embrace autonomy, make decisions, innovate valued solutions and drive results, providing you with exceptional personal and professional growth opportunities. No matter which of our seven segments or 80+ divisions you start in, you can grow your career at ITW.
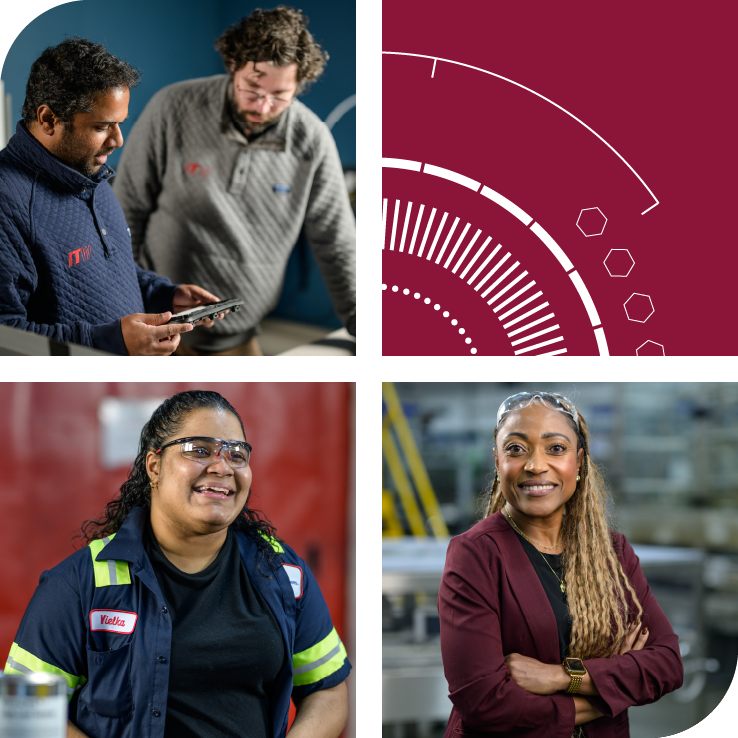
A sense of mutual respect and mindfulness permeates our culture-in fact, it’s the key to our success.
PRIDE IN HOW WE DELIVER.
At ITW, we’re proud of what we do and even more proud of how we do it. Our commitment to excellence and a unique approach to problem-solving empower us all to take pride in what they do and how do it.
We each have the support to think and act like entrepreneurs, to embrace autonomy, make decisions, and take ownership to create innovative solutions. This approach provides us with exceptional personal and professional growth opportunities.
Our focus on collaboration makes us collectively stronger and our committment to cultivating an inclusive environment where everyone can realize their full potential helps us thrive.
We use our reach and experience to invest in our people to grow through unique and relevant development opportunities. Regardless of the segment or division you start in, you can be assured of support and opportunity at every step.
It's more than a career it's pride in how you do it.
We each have the support to think and act like entrepreneurs, to embrace autonomy, make decisions, and take ownership to create innovative solutions. This approach provides us with exceptional personal and professional growth opportunities.
Our focus on collaboration makes us collectively stronger and our committment to cultivating an inclusive environment where everyone can realize their full potential helps us thrive.
We use our reach and experience to invest in our people to grow through unique and relevant development opportunities. Regardless of the segment or division you start in, you can be assured of support and opportunity at every step.
It's more than a career it's pride in how you do it.
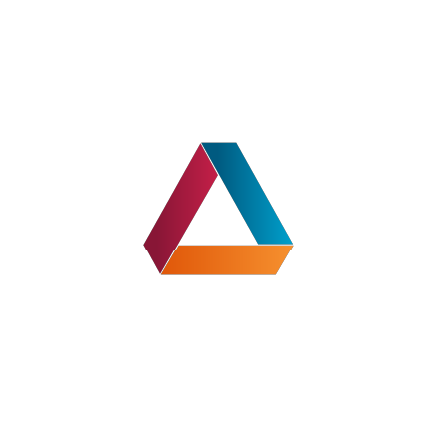
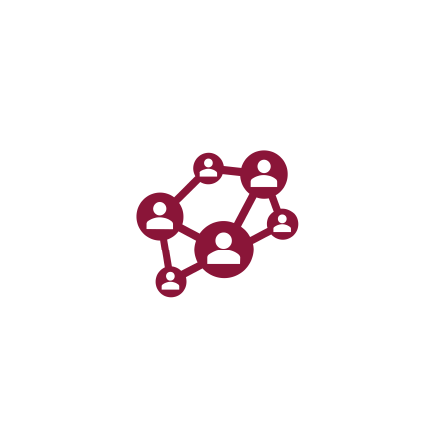
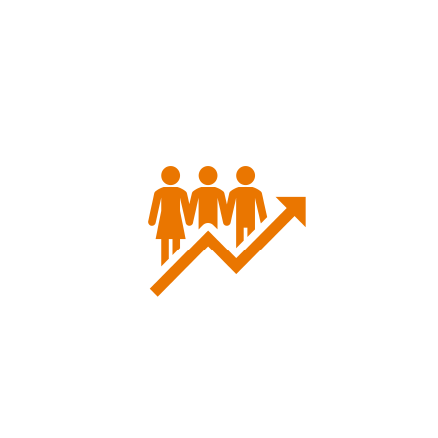
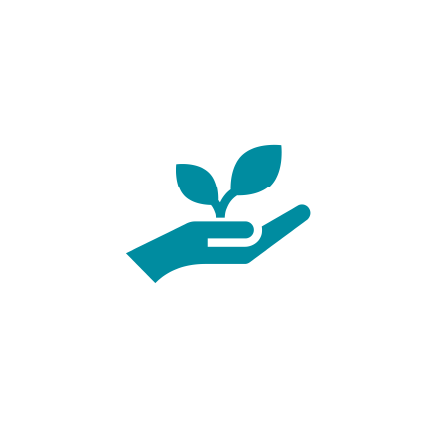
A sense of mutual respect and mindfulness permeates our culture-in fact, it’s the key to our success.
Why work here?
A sense of mutual respect and mindfulness permeates our culture-in fact, it’s the key to our success.
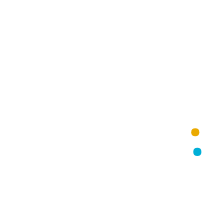
lorem ipsum
STAY CONNECTED TO ITW
Sign up for our Talent Community to receive updates as new opportunities become available.
A sense of mutual respect and mindfulness permeates our culture-in fact, it’s the key to our success.
Heading
There are many variations of passages of Lorem Ipsum available, but the majority have suffered alteration in some form, by injected humour, or randomised words which don't look even slightly believable.
CONNECTED BY THE ITW BUSINESS MODEL
Our goal to be one of the best performing, highest-quality and most respected industrial companies in the world is enabled by the hard work and dedication of our colleagues around the globe.
Watch the video to see how the ITW Business Model unites us.
Watch the video to see how the ITW Business Model unites us.
Heading
Lorem ipsum dolor sit amet consectetur adipisicing elit. Inventore assumenda asperiores distinctio est perferendis esse animi maiores dolor numquam nihil sint, et quae nobis harum consequuntur! Assumenda facere magnam nostrum?
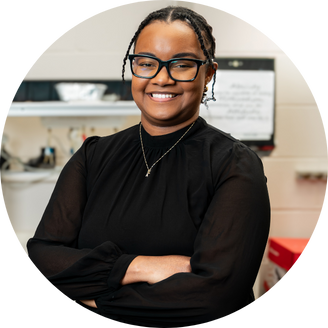
"ITW trusts their people and gives them opportunities to grow and develop. That encourages me to grow and strive to excel, and I hope I’m encouraging others to do the same along the way."
Ashley Lynch
Manufacturing Manager, ITW Medical
A sense of mutual respect and mindfulness permeates our culture-in fact, it’s the key to our success.
OUR BUSINESS SEGMENTS
We may not be a household name, but our impact is felt everywhere.
Our seven segments offer career opportunities in diverse, industry-leading businesses located in more than 50 countries, and our decentralized culture makes it possible to stay curious, develop your skills and learn new responsibilities.
Our seven segments offer career opportunities in diverse, industry-leading businesses located in more than 50 countries, and our decentralized culture makes it possible to stay curious, develop your skills and learn new responsibilities.
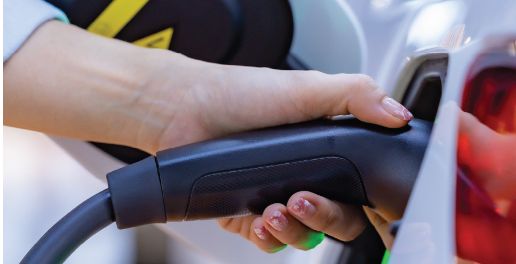
Meta
Automotive OEM
Life is more complicated than the simple binary of “work” and “life.” At Phenom Life is more complicated than the simple binary of work...
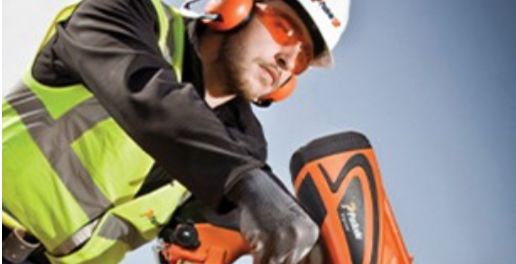
Meta
Construction Products
Life is more complicated than the simple binary of “work” and “life.” At Phenom Life is more complicated than the simple binary of work...
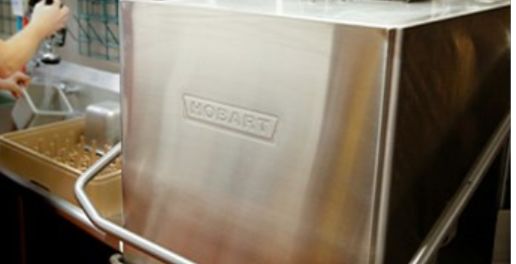
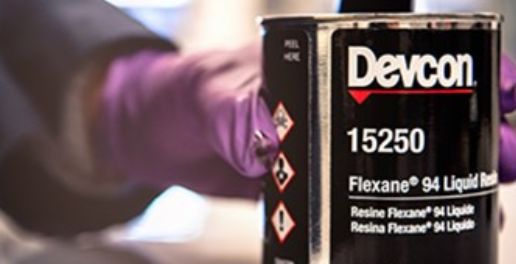
Meta
Polymers & Fluids
Life is more complicated than the simple binary of “work” and “life.” At Phenom Life is more complicated than the simple binary of work...
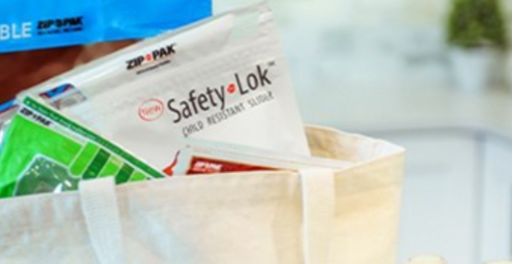
Meta
Specialty Products
Life is more complicated than the simple binary of “work” and “life.” At Phenom Life is more complicated than the simple binary of work...
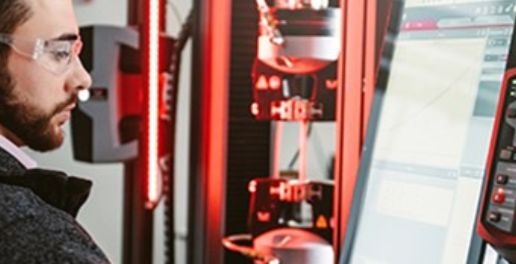
Meta
Test & Measurement and Electronics
Life is more complicated than the simple binary of “work” and “life.” At Phenom Life is more complicated than the simple binary of work...
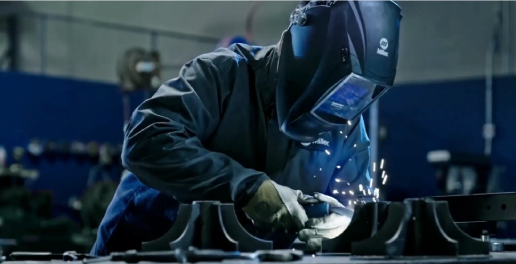
Meta
Welding
Life is more complicated than the simple binary of “work” and “life.” At Phenom Life is more complicated than the simple binary of work...
A sense of mutual respect and mindfulness permeates our culture-in fact, it's the key to our success.
Learn more
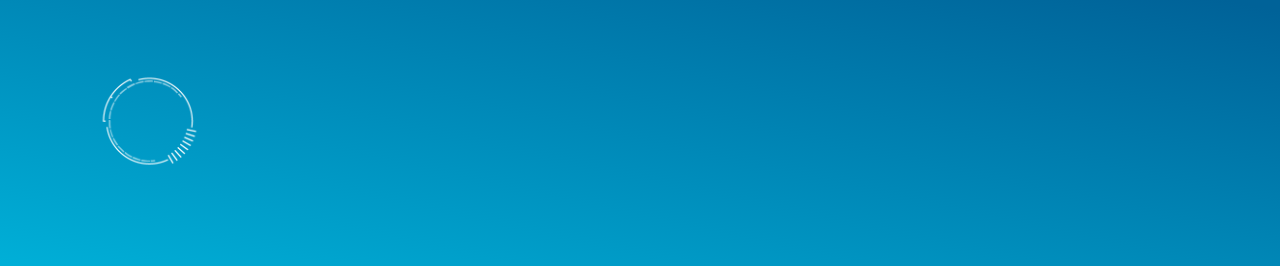
Find Opportunities to Ignite Your Full Potential
Blue gradient background